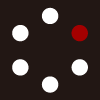
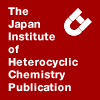
HETEROCYCLES
An International Journal for Reviews and Communications in Heterocyclic ChemistryWeb Edition ISSN: 1881-0942
Published online by The Japan Institute of Heterocyclic Chemistry
e-Journal
Full Text HTML
Received, 25th January, 2014, Accepted, 25th March, 2014, Published online, 3rd April, 2014.
DOI: 10.3987/COM-14-S(K)3
■ Pd/C-Catalyzed Hydrodechlorination of Dioxins from Fly Ash under Ambient Pressure and Temperature
Yasunari Monguchi,* Akiko Ido, Miki Niikawa, Nobuharu Nagatsu, Ryosuke Mizukoshi, Hisamitsu Nagase, and Hironao Sajiki*
Laboratory of Organic Chemistry, Department of Pharmaceutical Sciences, Gifu Pharmaceutical University, 1-25-4 Daigakunishi, Gifu 501-1196, Japan
Abstract
Dioxins, such as polychlorinated dibenzodioxins (PCDDs) and polychlorinated dibenzofurans (PCDFs), which could be efficiently extracted from fly ash based on the method approved by the Japanese Industrial Standard, were degraded by the palladium on carbon (Pd/C)-catalyzed hydrodechlorination in the presence of triethylamine at room temperature under ordinary pressure with a greater than 97% efficiency. The distinct features of the present degradation method of dioxins are its mildness, simplicity, safety, and efficiency without any expensive facilities.Polychlorinated dibenzo-p-dioxins (PCDDs), polychlorinated dibenzofurans (PCDFs), and dioxin-like polychlorinated biphenyls (DL-PCBs), which are generally abbreviated as dioxins (DXNs), are categorized into a particular class of persistent chlorinated organic pollutants due to the thermal, physical, and chemical stabilities (Figure 1). The toxicity of DXNs appears through their interaction with aryl hydrocarbon receptors in human cells, inducing a variety of biological responses, such as hormone signaling and gene expression.1 DXNs are produced as undesired byproducts during their course of waste Figure 1. Dioxins (DXNs)incineration at lower 1100 °C, steel manufacturing, ignition of engines, production of chlorinated agrochemicals, pharmaceuticals and industrial products, forest fires, volcanic activities, etc., in the presence of chlorine sources and are mainly contained in fly ash generated from waste incineration plants.1-3 Therefore, the development of a technology for the efficient degradation of DXNs in fly ash is an important issue, together with the reduction of DXNs in the incineration plants.
Recently developed methods for the DXNs degradation include thermal treatment at relatively low temperatures (140–600 °C),4-6 mechanochemical treatment,7 electrochemical reduction,8 photolysis,9 supercritical oxidation,10 biological treatment,11-14 reductive dechlorination using zelo-valent calcium,15 zinc,16 and iron metals,17 and transition metal-catalyzed hydrodechlorination.18-28 Transition metal-catalyzed hydrodechlorination methods, in particular, have achieved the effective degradation of DXNs under comparatively reasonable conditions, although highly moisture sensitive calcium metal,18,19 a strong base (NaOH),20-27 or supercritical CO2 (200 atm) together with 10 atm of H228 or flowing H2 gas26,27 is required.
We have developed a palladium on carbon (Pd/C)-catalyzed hydrodechlorination method of aromatic chlorides in MeOH at room temperature under ordinary hydrogen pressure in the presence of triethylamine (Et3N), which would work as a single electron donor to the palladium-activated chloroarenes in the early stage of the hydrodechlorination.29,30 The method was successfully and efficiently applied to the degradation of polychlorinated biphenyls (PCBs)31,32 and DDTs33 at room temperature into the corresponding harmless nonchlorinated arenes, and the practical utility was also demonstrated by a 50 L-pilot plant study of the PCBs degradation.34 Furthermore, the use of magnesium metal instead of Et3N was found to be quite effective for the PCBs degradation with35 or even without hydrogen gas (under nitrogen atmosphere).36
In this paper, the extraction of DXNs from fly ash generated in an industrial incinerator and the subsequent degradation of the extracted DXNs at room temperature under ordinary pressure based on the hydrodechlorination technology using the Pd/C–H2–Et3N combination are demonstrated. The efficiency of extraction and degradation of DXNs is discussed by the evaluation of the total toxicity equivalency quantity (TEQ) of seven PCDD congeners [one tetrachlorodibenzo-p-dioxin (TeCDD), one pentachlorodibenzo-p-dioxin (PeCDD), three hexachlorodibenzo-p-dioxins (HxCDDs), one heptachlorodibenzo-p-dioxin (HpCDD), and fully chlorinated octachlorodibenzo-p-dioxin (OCDD)] and twelve PCDF congeners [one tetrachlorodibenzofuran (TeCDF), three pentachlorodibenzofurans (PeCDFs), five hexachlorodibenzofurans (HxCDFs), two heptachlorodibenzofurans (HpCDFs), and fully
chlorinated octachlorodibenzofuran (OCDF)].
A highly effective, reliable, and simple method for DXNs extraction from fly ash would be needed for a smooth transition to the subsequent degradation process. The previous reports for the degradation of DXNs from fly ash adopted the Soxhlet extraction method using toluene as a most common solvent without any pretreatments,23-27 but the extraction efficiency was not described in these papers. We first examined the Soxhlet extraction of fly ash [0.25 ng-TEQ/g (the concentration was determined by the Japanese official method37,38 at the Chugai Technos Corporation), 20.0 g] generated from an incineration plant at Toyota Chemical Engineering Co., Ltd. using MeOH as an extraction solvent without any pretreatment, since MeOH was found to be the best solvent for the palladium on carbon (Pd/C)-catalyzed hydrodechlorination of aryl chlorides in the presence of Et3N under a H2 atmosphere;29,30 thus no change in the solvents for the degradation would be necessary after the extraction. A 17.01 g sample of fly ash in the extraction thimble placed in the Soxhlet extraction chamber was recovered after a 46-h extraction,39 and the DXNs concentration was measured to be 0.22 ng-TEQ/g (0.22 × 17.01 = 3.74 ng-TEQ). The extraction efficiency was calculated as the ratio of the extracted DXNs amounts to the DXNs content in the original fly ash before extraction (0.25 × 20.0 = 5.00 ng-TEQ) according to Eq. (1), in which the extracted DXNs amounts refer to the subtraction of the DXNs content in the fly ash obtained from the extraction thimble after extraction from the DXNs content in the original fly ash before extraction. Unfortunately, only a 25.2% [(5.00–3.74)/5.00 × 100] extraction efficiency was achieved, indicating that MeOH was not a suitable solvent for the Soxhlet extraction of DXNs from fly ash. Toluene was then used instead of MeOH, since several previous reports used it for the Soxhlet extraction solvent of fly ash contaminated with DXNs.23-27 However, the DXNs were not sufficiently extracted (only 49.2% extraction efficiency). The HCl pretreatment of fly ash and subsequent Soxhlet extraction were then examined according to the Japanese official method.37,38 The pretreatment would open the pore structure of fly ash particles, and then the solvent for the Soxhlet extraction could approach their inside leading to an increase of the extraction efficiency.40-42 A 10.0 g sample of fly ash (0.25 ng-TEQ/g, 2.50 ng-TEQ) was pretreated with 2M HCl for 1 h, then the mixture was filtered. A part of the DXNs was extracted from the aqueous filtrate with CH2Cl2, and the other part was extracted from the solid residue on the filter paper using a Soxhlet extractor with toluene for 24 h. The CH2Cl2 and Soxhlet extracts were combined and concentrated in vacuo (DXNs concentration of the extracts was 34 ng-TEQ/g). The DXNs concentration in the solid fly ash (1.4468 g) in the thimble after the Soxhlet extraction was measured to be 0.043 ng-TEQ/g. The high extraction efficiency, which was calculated as 97.5% [(2.50–0.043 × 1.4468)/2.50 × 100], was observed. Therefore, the method based on the Japanese official method37,38 was adopted for the DXNs extraction from fly ash before the DXNs degradation.
The degradation of the DXNs in MeOH extract [without HCl pretreatment, 1.50 g, 520 pg-TEQ/g, 780 pg-TEQ, see total (PCDDs + PCDFs) for the extracted DXNs before hydrodechlorination in Table 1, Run 1] was first investigated at room temperature using 10% Pd/C (10 wt% of the extract) and Et3N under ordinary H2 conditions (Table 1, Run 1). After 24 h of stirring, the catalyst was removed by filtration, and the resulting filtrate was concentrated. Since 0.12 pg-TEQ/g of the DXNs was detected from the residue [0.701 g, see total (PCDDs + PCDFs) for the DXNs in the residue after hydrodechlorination in Table 1, Run 1], the degradation efficiency was determined greater than 99.9% [(78 –0.12 × 0.701)/780 × 100] on the basis of Eq. (2), indicating that the DXNs could be efficiently hydrodechlorinated. Similarly, DXNs in the toluene extract (without HCl pretreatment, 720 pg-TEQ), could be degraded to the level of no detection of DXNs, Table 1, Run 2]. The combined use of Pd/C and Et3N could successfully achieved the hydrodechlorination of polychlorinated oxygen-containing heterocycles, such as polychlorinated dibenzo-p-dioxanes and dibenzofurans, under ambient pressure and temperature. The oxygen atoms and planar (non-twisted) aromatic ring system of PCDDs and PCDFs would facilitate the approach of palladium metal to the aromatic nuclei by the coordination of oxygen atoms and obstruction-free interaction with arenes. The aromatic ring activated by the palladium metal would easily undergo the electron transfer from Et3N or palladium metal, and the hydrodechlorination would readily take place.
We next investigated the successive extraction of the DXNs from 10.0 g fly ash (250 pg-TEQ/g, 2500 pg-TEQ) and degradation by the Pd/C-catalyzed hydrodechlorination in the presence of Et3N to establish an efficient method for the remediation of fly ash from the DXNs (Table 2). The 2M HCl-pretreated fly ash was applied to the Soxhlet extraction with toluene, and the aqueous filtrate was extracted with CH2Cl2. The extraction was found to be effectively carried out, and the extraction efficiency (98.5%) was determined according to Eq. (1) based on the DXNs concentration in the fly ash (1.5464 g) obtained from the extraction thimble after Soxhlet extraction [24 pg-TEQ/g, see total (PCDDs + PCDFs) for the DXNs in fly ash after extraction in Table 2]. The Soxhlet extract and CH2Cl2 extract were combined, concentrated, dried (83.3 mg), and subjected to analysis of the DXNs [41000 pg-TEQ/g, see total (PCDDs + PCDFs) for the DXNs before hydrodechlorination in Table 2]. A part of the extracts (41.0 mg, 41000 × 0.0410 = 1681 pg-TEQ) was used for the degradation experiment. The extract in MeOH was stirred under an ordinary H2 atmosphere at room temperature for 24 h together with 10% Pd/C and Et3N. The mixture was filtered to remove the 10% Pd/C, and the filtrate was concentrated under reduced pressure. The DXNs concentration in the residue (26.0 mg) was measured to be 1700 pg-TEQ/g [see total (PCDDs + PCDFs) for the DXNs in the residue after hydrodechlorination in Table 2], indicating that a 97.4% degradation efficiency was achieved [(1681–1700 × 0.026)/1681 × 100].
In conclusion, we have developed an efficient degradation method for DXNs (PCDDs and PCDFs) extracted from fly ash. The acidic pretreatment of fly ash before Soxhlet extraction with toluene was an indispensible process for the effective removal of the DXNs from fly ash, although the process was skipped in many cases in the literature. The Pd/C–H2–Et3N combination could efficiently hydrodechlorinate the extracted DXNs (PCDDs and PCDFs) at room temperature under ordinary hydrogen pressure. One of distinguished features of the present method is no requirements of special equipment because of the effective degradation under such mild conditions.
EXPERIMENTAL
Materials
MeOH, toluene, and hexane were purchased as HPLC grade from Wako Pure Chemical Industries, Ltd. (Osaka, Japan). 10% Pd/C (k-type, dry) and Et3N were obtained from N. E. Chemcat Corporation (Tokyo, Japan) and Wako Pure Chemical Industries, Ltd., respectively. Fly ash was obtained from the incineration plant of Toyota Chemical Engineering Co., Ltd. The DXNs' concentration in the fly ash was determined to be 0.25 ng-TEQ/g, which was below Japan's domestic standards for DXNs in fly ash (<3 ng-TEQ/g), by the extraction and HRGC–HRMS analysis.37,38 All other reagents were purchased from commercial sources and used without further purification.
Analysis
All analyses of the DXNs (TEQ/g) were carried out at the Chugai Technos Corporation (Hiroshima, Japan) in compliance with the Japanese official methods for the disposal standard of specially controlled general and industrial wastes established by the Japanese Ministry of Health and Welfare (Notification No. 192, 1992)37 and the method for determination of tetra-through-octachlorobenzo-p-dioxins, tetra-through-octachlorodibenzofurans and dioxin-like polychlorinated biphenyls in stationary source emissions [Japanese Industrial Standards (JIS) K 0311].38
The sample was treated with 2M HCl and filtered. The solid residue was extracted using a Soxhlet extractor with toluene for over 16 h, and the aqueous filtrate was extracted three times with CH2Cl2. The combined extracts were concentrated, and the cleanup spike [13C labelled internal standard solution of PCDDs/PCDFs (DF-LCS-A, Wellington Laboratories Inc., Ontario, Canada) and DL-PCBs (PCB-LCS-A1, Wellington Laboratories Inc.)] was added. The mixture was purified by chromatography using cleanup cartridge columns of multi-layer silica gel (GL Sciences Inc., Tokyo Japan) and two-layer carbon silica gel (GL Sciences Inc.) to afford three fractions, the first of which contained hydrocarbons and was stored. The second and third fractions contained DL-PCBs and PCDDs/PCDFs, respectively. These two fractions were analyzed by HRGC–HRMS using an Agilent 6890/Thermo Trace GC instrument after the addition of a syringe spike [13C labelled internal standard solution of DL-PCBs (PCB-IS-B, Wellington Laboratories, Inc.) for the second fraction and PCDDs/PCDFs (DF-IS-I, Wellington Laboratories, Inc.) for the third fraction].
The analysis conditions were as follows for the DL-PCBs (data were not shown): column, HT8-PCB (Cica) 60 m × 0.25 mm ID; carrier gas, He; injection temperature, 280 °C; splitless (60 sec); oven temperature, to ramp from 110 °C (1 min hold) to 200 °C at the rate of 20 °C/min, then to 240 °C (0 min hold) at the rate of 2 °C/min, and to 300 °C (0 min hold) at the rate of 8 °C/min; MS (EI, positive); for the PCDDs/PCDFs (Te–HxCDD/DF): column, SP-2331 (Supelco) 60 m × 0.32 mm ID, 0.20 μm; carrier gas, He; injection temperature, 250 °C; splitless (60 sec); oven temperature, to ramp from 110 °C (1 min) to 200 °C (1 min hold) at the rate of 20 °C/min then to 250 °C at the rate of 4 °C/min; MS (EI, positive); for the PCDDs/PCDFs (1,2,3,7,8,9-HxCDD, Hp–OCDD/DF): column, DB-17 (J & W) 30 m × 0.32 mm ID, 0.25 μm; carrier gas, He; injection temperature, 280 °C; splitless (60 sec); oven temperature, to ramp from 110 °C (1 min hold) to 200 °C (0 min) at the rate of 20 °C/min, then to 280 °C at the rate of 3 °C/min; MS (EI, positive).
Extraction of DXNs from fly ash
Soxhlet extraction of fly ash without pretreatments
From MeOH: The Soxhlet extraction of fly ash (20.0 g, 0.25 ng-TEQ/g, 5.00 ng-TEQ) was carried out using MeOH (1 L) for 46 h. The DXNs concentration in the fly ash (17.01 g) obtained from the extraction thimble after the Soxhlet extraction was analyzed to be 0.22 ng-TEQ/g (3.74 ng-TEQ). The extract efficiency was calculated to be 25.2%, according to Eq. (1). The Soxhlet MeOH extract was concentrated to give a solid residue (2.99 g, the residue includes MeOH-soluble impurities). A part of the residue (1.49 g) was used for the analysis of the DXNs in the residue [0.52 ng-TEQ/g; 0.52 × 2.99 (g, weight of total Soxhlet extract) = 1.55 ng-TEQ], and the other part (1.50 g, 0.780 ng-TEQ) was used for the hydrodechlorination (see Table 1, Run 1). The total amount of DXNs obtained from the fly ash after the Soxhlet extraction (3.74 ng-TEQ) and DXNs in the Soxhlet extract (1.55 ng-TEQ) is virtually the same as the DXNs content in the original fly ash (5.00 ng-TEQ).
From toluene: The Soxhlet extraction of fly ash (20.0 g, 5.00 ng-TEQ) was carried out using toluene (1.3 L) for 24 h. The DXNs concentration in the fly ash residue (19.57 g) obtained from the extraction thimble after the Soxhlet extraction was analyzed to be 0.13 ng-TEQ/g (0.13 × 19.57 = 2.54 ng-TEQ). The extract efficiency was calculated to be 49.2% [(5.00–2.54)/5.00 × 100] according to Eq. (1). The Soxhlet toluene extract was concentrated to give a solid residue (430 mg). A part of the residue (250 mg) was used for the analysis of the DXNs in the residue [4.0 ng-TEQ/g, 4.0 × 0.430 (g, weight of total Soxhlet extract) = 1.72 ng-TEQ), and the other part (180 mg, 0.720 ng-TEQ) was used for the hydrodechlorination (see Table 1, Run 2). The total amount of DXNs obtained from the fly ash after the Soxhlet extraction (2.54 ng-TEQ) and DXNs in the Soxhlet extract (1.72 ng-TEQ) are quite low. The error (15%) might arise from the nonuniform distribution of the DXNs in the original fly ash.
Soxhlet extraction of fly ash with acid pretreatment
10.0 g of fly ash (0.25 ng-TEQ/g, 2.50 ng-TEQ) were placed in a 500 mL Erlenmeyer flask and 2M HCl (240 mL) was added. The mixture was gently stirred and filtered using filter paper (4 μm). The solid residue on the filter paper was successively washed with H2O (20 mL × 4) and MeOH (5 mL × 5). The filtrate was extracted with CH2Cl2 (200 mL × 5), and the combined CH2Cl2 layers were concentrated. The Soxhlet extraction of the solid residue on the filter paper was carried out using toluene (1.2 L) for 24 h. The DXNs concentration in the fly ash (1.4468 g) obtained from the extraction thimble after the Soxhlet extraction was analyzed to be 0.043 ng-TEQ/g (0.043 × 1.4468 = 0.0622 ng-TEQ). The extract efficiency was calculated to be 97.5% according to Eq. (1). The DXNs concentration of the combined Soxhlet and CH2Cl2 extracts (89.4 mg) was 34 ng-TEQ/g [3.04 ng-TEQ (34 × 0.0894)] after concentration in vacuo. Although the total amount of DXNs obtained after the extraction [3.10 ng-TEQ (0.0622 + 3.04)] exceeded the DXNs content in the original fly ash (2.50 ng-TEQ), the error (24%) might arise from the nonuniform distribution of the DXNs in the original fly ash.
Degradation of DXNs (Table 1)
Run 1: A mixture of DXNs extract from MeOH (1.50 g, the extract includes MeOH-soluble impurities, 0.52 ng-TEQ/g, 0.780 ng-TEQ), 10% Pd/C (45.0 mg, 10 wt% of DXNs extract), and Et3N (2.60 mL, 18.6 mmol) in MeOH (20 mL) was stirred at room temperature under a H2 atmosphere (balloon) for 24 h, filtered through a 0.45 µm membrane filter (Millipore, USA), and the solid residue was washed with MeOH (5 mL × 5). The combined filtrates were concentrated, and the DXNs concentration in the residue (701 mg) was measured to be 0.00012 ng-TEQ/g (0.00012 × 0.701 = 0.0000841 ng-TEQ) at the Chugai Technos Corporation. The degradation efficiency was determined as >99.9% [(0.780–0.0000841)/0.780 × 100] according to Eq. (2).
Run 2: A mixture of DXNs extract from toluene (180 mg, 4.0 ng-TEQ/g, 0.720 ng-TEQ), 10% Pd/C (18.0 mg, 10 wt% of DXNs extract), and Et3N (467 μL, 3.35 mmol) in MeOH (10 mL) was stirred at room temperature under a H2 atmosphere (balloon) for 24 h, then filtered through a 0.45 µm membrane filter (Millipore) and the solid residue was washed with MeOH (5 mL × 5). The combined filtrates were concentrated, and DXNs were not detected in the residue (148 mg). The degradation efficiency was determined as >99.9%.
Successive extraction and degradation of DXNs from fly ash (Table 2)
10.0 g of fly ash (0.25 ng-TEQ/g, 2.50 ng-TEQ) was placed in a 500 mL Erlenmeyer flask and 2M HCl (240 mL) was added. The mixture was gently stirred and filtered using filter paper (4 μm). The solid residue on the filter paper was successively washed with H2O (20 mL × 4) and MeOH (5 mL × 5). The filtrate was extracted with CH2Cl2 (200 mL × 5) and the combined CH2Cl2 layers were concentrated. The Soxhlet extraction of the solid residue on the filter paper was carried out using toluene (1.2 L) for 31 h. The DXNs concentration in the fly ash (1.5464 g) obtained from the extraction thimble after the Soxhlet extraction was measured to be 0.024 ng-TEQ/g (0.024 × 1.5464 = 0.0371 ng-TEQ, extraction efficiency, 98.5%). The Soxhlet toluene extract and CH2Cl2 extract were combined and concentrated in vacuo to give a residue (83.3 mg), the DXNs concentration of which was measured to be 41 ng-TEQ/g [3.42 ng-TEQ (41× 0.0833)]. Although the total amount of DXNs obtained after the extraction [3.46 ng-TEQ (0.0371 + 3.42)] exceeded the DXNs content in the original fly ash (2.50 ng-TEQ), the error (38%) might arise from the nonuniform distribution of DXNs in the original fly ash.
A mixture of DXNs extract (41.0 mg, 41 ng-TEQ/g, 1.68 ng-TEQ), 10% Pd/C (4.1 mg), and Et3N (85.3 μL, 612 μmol) in MeOH (5 mL) was stirred at room temperature under a H2 atmosphere (balloon) for 24 h, then filtered through a 0.45 µm membrane filter (Millipore), and the solid residue was washed with MeOH (5 mL × 5). The combined filtrates were concentrated, and the DXNs concentration in the residue (26.0 mg) was determined to be 1.7 ng-TEQ/g (1.7 × 0.0260 = 0.0442 ng-TEQ). The degradation efficiency was analyzed to be 97.4% [(1.68–0.0442)/1.68 × 100].
ACKNOWLEDGEMENTS
We sincerely appreciate the partial support by the New Energy and Industrial Technology Development Organization (NEDO), Japan. We thank N.E. Chemcat Corporation for the kind gift of the 10% Pd/C.
References
1. P. S. Kulkarni, J. G. Crespo, and C. A. M. Afonso, Environ. Int., 2008, 34, 139. CrossRef
2. M. Altarawneh, B. Z. Dlugogorski, E. M. Kennedy, and J. C. Mackie, Prog. Energ. Combust., 2009, 35, 245. CrossRef
3. T. Shibamoto, A. Yasuhara, and T. Katami, Rev. Environ. Contam. Toxicol., 2007, 190, 1. CrossRef
4. Y. Ide, K. Kashiwabara, S. Okada, T. Mori, and M. Hara, Chemosphere, 1996, 32, 189. CrossRef
5. E. V. de Pava and E. Battistel, Chemosphere, 2005, 59, 1333. CrossRef
6. G.-J. Song, S. H. Kim, Y.-C. Seo, and S.-C. Kim, Chemosphere, 2008, 71, 248. CrossRef
7. Y. Nomura, S. Nakai, and M. Hosomi, Environ. Sci. Technol., 2005, 39, 3799. CrossRef
8. K. Miyoshi, Y. Kamegaya, and M. Matsumura, Chemosphere, 2004, 56, 187. CrossRef
9. A. L. McPeters and M. R. Overcash, Chemosphere, 1993, 27, 1221. CrossRef
10. T. Sako, T. Sugeta, K. Otake, M. Sato, M. Tsugumi, T. Hiaki, and M. Hongo, J. Chem. Eng. Jpn., 1997, 30, 744. CrossRef
11. I.-H. Nam, H.-B. Hong, Y.-M. Kim, B.-H. Kim, K. Murugesan, and Y.-S. Chang, Water Res., 2005, 39, 4651. CrossRef
12. K. Ishii and T. Furuichi, J. Hazard. Mater., 2007, 148, 693. CrossRef
13. I. Kamei, M. Watanabe, K. Harada, T. Miyahara, S. Suzuki, Y. Matsufuji, and R. Kondo, Chemosphere, 2009, 75, 1294. CrossRef
14. Y. Suzuki, M. Nakamura, Y. Otsuka, N. Suzuki, K. Ohyama, T. Kawakami, K. Sato, S. Kajita, S. Hishiyama, A. Takahashi, and Y. Katayama, Environ. Toxicol. Chem., 2012, 31, 1072. CrossRef
15. Y. Mitoma, T. Uda, N. Egashira, C. Simion, H. Tashiro, M. Tashiro, and X. Fan, Environ. Sci. Technol., 2004, 38, 1216. CrossRef
16. Z. Wang, W. Huang, D. E. Fennel, and P. Peng, Chemosphere, 2008, 71, 360. CrossRef
17. J.-H. Kim, P. G. Tratnyek, and Y.-S. Chang, Environ. Sci. Technol., 2008, 42, 4106. CrossRef
18. Y. Mitoma, M. Takase, Y. Yoshino, T. Masuda, H. Tashiro, N. Egashira, and T. Oki, Environ. Chem., 2006, 3, 215. CrossRef
19. Y. Mitoma, N. Tasaka, M. Takase, T. Masuda, H. Tashiro, N. Egashira, and T. Oki, Environ. Sci. Technol., 2006, 40, 1849. CrossRef
20. Y. Ukisu and T. Miyadera, Chemosphere, 2002, 46, 507. CrossRef
21. Y. Ukisu and T. Miyadera, Appl. Catal. B, 2003, 40, 141. CrossRef
22. Y. Ukisu and T. Miyadera, Appl. Catal. A, 2004, 271, 165. CrossRef
23. M. Cobo, A. Quintero, and C. M. de Correa, Catal. Today, 2008, 133–135, 509. CrossRef
24. M. Cobo, J. A. Conesa, and C. M. de Correa, Appl. Catal. B, 2009, 92, 367. CrossRef
25. Z. Yang, C. Xia, Q. Zhang, J. Chen, and X. Liang, Waste Manage., 2007, 27, 588. CrossRef
26. F. Zhang, J. Chen, H. Zhang, Y. Ni, and X. Liang, Chemosphere, 2007, 68, 1716. CrossRef
27. F. Zhang, J. Chen, H. Zhang, Y. Ni, Q. Zhang, and X. Liang, Sep. Purif. Technol., 2008, 59, 164. CrossRef
28. B.-Z. Wu, H.-Y. Chen, J. S. Wang, C.-S. Tan, C. M. Wai, W. Liao, and K.-H. Chiu, J. Hazard. Mater., 2012, 227–228, 18. CrossRef
29. H. Sajiki, A. Kume, K. Hattori, and K. Hirota, Tetrahedron Lett., 2002, 43, 7247. CrossRef
30. Y. Monguchi, A. Kume, K. Hattori, T. Maegawa, and H. Sajiki, Tetrahedron, 2006, 62, 7926. CrossRef
31. H. Sajiki, A. Kume, K. Hattori, H. Nagase, and K. Hirota, Tetrahedron Lett., 2002, 43, 7251. CrossRef
32. A. Kume, Y. Monguchi, K. Hattori, H. Nagase, and H. Sajiki, Appl. Catal. B, 2008, 81, 274. CrossRef
33. Y. Monguchi, A. Kume, and H. Sajiki, Tetrahedron, 2006, 62, 8384. CrossRef
34. Y. Monguchi, S. Ishihara, A. Ido, M. Niikawa, K. Kamiya, Y. Sawama, H. Nagase, and H. Sajiki, Org. Process Res. Dev., 2010, 14, 1140. CrossRef
35. A. Ido, S. Ishihara, A. Kume, T. Nakanishi, Y. Monguchi, H. Sajiki, and H. Nagase, Chemosphere, 2013, 90, 57. CrossRef
36. S. Ishihara, A. Ido, Y. Monguchi, H. Nagase, and H. Sajiki, J. Hazard. Mater., 2012, 229–230, 15. CrossRef
37. The disposal standard of specially controlled general and industrial wastes. Ministry of Health and Welfare, Notification No. 192, 1992, http://www.env.go.jp/hourei/syousai.php?id=11000314 (in Japanese, accessed 25.2.2014), see the analysis part in the experimental section.
38. Method for determination of tetra-through octachlorodibenzo-p-dioxins, tetra-through octachlorodibenzofurans and dioxin-like polychlorinatedbiphenyls in stationary source emissions. Japanese Industrial Standards (JIS) K 0311, 1995, http://www.jisc.go.jp/app/pager?id=446929 (in Japanese, accessed 25.2.2014), see the analysis part in the experimental section.
39. The prolonged extraction time (46 h) was adopted to increase the extraction efficiency in the light of the low hydrophobic nature of MeOH.
40. R. M. M. Kooke, J. W. A. Lustenhouwer, K. Olie, and O. Hutzinger, Anal. Chem., 1981, 53, 461. CrossRef
41. L. Stieglitz, G. Zwick, and W. Roth, Chemosphere, 1986, 15, 1135. CrossRef
42. K. Takayama, H. Miyata, M. Mimura, J. Ogaki, and T. Kashimoto, Eisei Kagaku, 1988, 34, 231. CrossRef