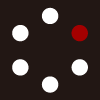
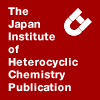
HETEROCYCLES
An International Journal for Reviews and Communications in Heterocyclic ChemistryWeb Edition ISSN: 1881-0942
Published online by The Japan Institute of Heterocyclic Chemistry
e-Journal
Full Text HTML
Received, 5th June, 2014, Accepted, 29th July, 2014, Published online, 13th August, 2014.
DOI: 10.3987/COM-14-S(K)37
■ New Approach to Cyclophanes Containing Ethyleneoxy Bridge by Glaser–Eglinton Coupling
Sambasivarao Kotha* and Gopalkrushna T. Waghule
Department of Chemistry, Indian Institute of Technology Bombay, Powai, Mumbai - 400076, India
Abstract
Three strategies have been explored to generate cyclophane derivatives. In this regard, we identified alkyne metathesis, Diels–Alder reaction, and Glaser–Eglinton coupling as key steps. To this end, cyclophane derivatives containing ethyleneoxy bridge were successfully synthesized in four steps involving Glaser–Eglinton coupling and catalytic hydrogenation sequence.Among macrocycles, crown ethers play a critical role in molecular recognition,1-7 metal ion transportation,8 and also in drug design.9,10 Synthesis of cyclophanes containing crown ether moiety is a difficult task because the synthetic processes leads to the formation of oligomers and the required products are formed in low yield.11,12 Among other macrocycles, cyclophane13-21 synthesis is of great interest because of the presence of aromatic rings that are linked together by aliphatic chains in a cyclic manner. Due to this structural sophistication, cyclophanes with a defined cavity size is useful in encapsulating and also stabilizing selective guest molecules. For this reason, larger cyclophanes provide a cavity fit for complex metal ions, or they can accommodate bulky guest molecules. To this end, design of new synthetic methods to cyclophanes of varying cavity size and shape is an important exercise. Moreover, introducing diverse functional groups or hetero atoms at an appropriate site(s) of the cyclophane moiety can bring structural variations desirable for molecular recognition. In connection with a major program aimed at designing new routes to cyclophanes,22-27 we have shown that the crown containing compound 1 is useful to generate the diene 2 by cross-enyne metathesis sequence (Figure 1). Later the diene 2 was found to be useful starting material to various cyclophane derivatives via the Diels–Alder (DA) strategy.28,29 Here, we identified o-xylylene intermediate 3 containing crown ether moiety and the dialkyne building block 4 for further synthetic exploration. In this short paper, we report our results in this direction.
To design functionalized cyclophanes, we conceived three different strategies. The first one involves alkyne metathesis of 6 and the second one deals with the DA reaction of the o-xylylene intermediate such as 3 (Figure 2). The third route relies on Glaser–Eglinton coupling30 reaction of dialkyne 6 to generate the cyclophane derivatives 4.
Alkyne metathesis31-38 is a valuable strategy to prepare macrocycles. To explore new routes to cyclophane derivatives, initially we attempted the alkyne metathesis of 8 to assemble macrocyclic compound 1. In this regard, bisphenol 5 was reacted with propargyl bromide under K2CO3/acetone reflux condition to generate the dipropargylated compound 6 in 86% yield (Scheme 1). Then, the acidic hydrogens present on terminal alkyne portion of 6 were replaced with methyl groups by using n-BuLi/MeI/THF conditions to generate the dimethyl compound 8 in 68% yield.
Next, the diacetylene derivative 8 was subjected to alkyne metathesis in the presence of homogeneous catalyst such as Mo(CO)6/4-chlorophenol in refluxing chlorobenzene for 12 h. However, our attempts to generate the corresponding metathesis product 1 were unsuccessful, and the starting material 8 was recovered.
Another approach to produce catechol-type crownophane derivatives such as 15 involve treatment of the dibromide 1139 with rongalite40-44 to generate sulfone 14, which can undergo a DA reaction with a suitable dienophiles followed by aromatization sequence. In this regard, the diester 928 was reduced with an excess amount of lithium aluminium hydride (LAH) in dry THF under reflux conditions to deliver the diol 10 (62% yield). Later, conversion of the diol 10 to the corresponding dibromide 11 was attempted using various brominating reagents such as PBr3 in dry DCM. Unfortunately, durene tetrabromide was obtained in 76% yield instead of the expected dibromide 11 (Scheme 2). Alternatively, when the diol 10 was subjected to using BF3∙OEt2/NaBr bromination conditions, only mono-bromoderivative was obtained and all other attempts to convert the monobromide to the dibromide 11 were unsuccessful.
Next, we prepared the dibromide 11 by adopting the known procedure.39 The yield of the dibromo compound 11 is 24% and later the dibromide 11 was treated with rongalite in the presence of phase-transfer catalyst (PTC) such as tetra-n-butylammonium bromide (TBAB) to generate the sulfone 14 in 51% yield. Subsequently, the sulphone 14 was treated with dimethylacetylene dicarboxylate (DMAD) under toluene reflux conditions to generate the DA adduct. However, under these condition no DA product was obtained and the starting material was recovered. Even under forcing reaction conditions no DA product was obtained. Further, when the DA reaction of 14 with DMAD was attempted under microwave conditions no desired DA adduct was obtained (Scheme 3).
Our next route to prepare cyclophanes involves, O-propargylation followed by Glaser–Eglinton coupling and hydrogenation reaction sequences. In this regard, the dipropargylated compound 6 was subjected to Glaser–Eglinton coupling strategy to generate the macrocyclic bis-acetylene derivative 4 in 94% yield (Scheme 4).
Finally, the diyne 4 was subjected to hydrogenation sequence with 10% Pd/C under 1 atm. pressure of H2 to generate the cyclophane derivative 7 in 92% yield. Alternatively, the cyclophane 7 was also obtained by treatment of the bisphenol 5 with 1,6-dibromohexane in the presence of K2CO3 under acetonitrile reflux condition in 56% yield.
Along similar lines, bisphenol derivative 12,45 was converted to the corresponding O-propargylated compound 16 in 84% yield on reaction with propargyl bromide in the presence of K2CO3 under acetone reflux condition (Scheme 5). Further, the dipropargyl derivative 16 was reacted with Cu-II salt in the presence of pyridine to generate a cyclic conjugated macrocycle 17 in 81% yield. Hydrogenation of the dialkyne 17 in the presence of 10% Pd/C under H2 atmosphere gave the cyclophane derivative 18 in 90% yield. In another route, bisphenol 12 was alkylated with 1,6-dibromohexane in the presence of K2CO3 to deliver 18 in 50% yield.
In conclusion, we have designed a simple strategy for the synthesis of cyclophane derivatives 7 and 18 by using Glaser–Eglinton coupling and catalytic hydrogenation as key steps. Synthesis of 7 and 18 was carried under normal concentration without using high dilution conditions. This may be due to the presence of ethyleneonxy linkage which provide close proximity for O-propargyl group and help for Glaiser–Eglinton coupling. This protocol may be extended to variety of other cyclophane derivatives by varying the length of alkynyl moiety attached to bisphenols 12 (or 5). Several intermediates prepared here (e.g. 4 and 17) may play an influential role in exploring new strategies to cyclophane derivatives containing ethyleneoxy bridge of varying chain length.
EXPERIMENTAL
Synthesis of sulfone 14
To a suspension of rongalite (1.18 g, 9.5 mmol) in DMF (15 mL) were added TBAB (305 mg, 0.95 mmol) and dibromide compound 11 (550 mg, 0.95 mmol) at 0 oC, and the stirring was continued for 4 h at 0 oC. Then, the reaction mixture was brought to rt, and the stirring was continued for an additional 4 h. After completion of the reaction (TLC monitoring), the reaction mixture was diluted with EtOAc and washed with water (3-4 times). The aqueous layer was again extracted with 30 mL of EtOAc and the combined organic layer was washed with brine, dried over Na2SO4, and concentrated under reduced pressure, and the product was purified by silica gel column chromatography. Elution of the column with 70% EtOAc/ petroleum ether gave 14.
Compound 14 colorless solid: Rf = 0.3 in (70% EtOAc/ petroleum ether mixture): (234 mg, 51% yield); mp 210 oC; 1H NMR (400 MHz, CDCl3): δ 3.85 (t, J = 4.08 Hz, 4H), 4.15 (t, J = 4.00 Hz, 4H), 4.40 (s, 4H), 5.21 ( s, 4H), 7.04−6.87 ( m, 10 H); 13C NMR (100 MHz, CDCl3): δ = 57.13, 67.95, 69.67, 70.45, 113.15, 119.46, 121.25, 123.71, 125.56, 130.63, 137.16, 148.00, 150.84; HRMS (Q-TOF) m/z: [M+Na]+ calcd for C26H26O7SNa 505.1296 found 505.1298; IR (KBr): υmax 1265, 1422, 1602, 2305, 2986, 3434 cm-1.
General procedure for O-propargylation
To a stirred solution of bisphenol (5/12) (1 mmol) in acetone (15 mL) was added K2CO3 (5 mmol) and the resultant suspension was stirred for 30 min. Then, propargyl bromide (3 mmol) was added dropwise over a period of 10 min. Further, the crude reaction mixture was stirred for 12 h at reflux. At the conclusion of the reaction (TLC monitoring), the crude mixture was filtered through celite pad (washed with CH2Cl2) and concentrated under reduced pressure. The crude product was purified by column chromatography.
Following the general procedure, 1 mmol (290 mg) of bisphenol 5 was subjected to O-propargylation to generate compound 6 (314 mg, 86% yield). Compound 6 has been obtained by elution of the column with 10% EtOAc/petroleum ether.
Data for compound 6 Rf = 0.4 in (10% EtOAc/ petroleum ether mixture): colorless solid: mp 120 oC; 1H NMR (400 MHz, CDCl3): δ 2.51 (t, J = 2.5 Hz, 2H), 3.91-3.93 (m, 4H), 4.13-4.15 (m, 4H), 4.65 (d, J = 2.5 Hz, 4H), 6.90-7.25 (m, 8H); 13C NMR (100 MHz, CDCl3): δ 56.01, 67.68, 70.07, 75.69, 78.71, 102.28, 107.49, 107.95, 130.08, 158.91, 160.11; HRMS (Q- TOF) m/z: [M+Na]+ calcd for C22H22O5Na 389.1359 found 389.1357; IR (KBr): υmax 740, 1265, 1422, 1602, 2305, 2986, 3434 cm-1.
Following the general procedure, 1 mmol (290 mg) of bisphenol 12 was subjected for O-propargylation to generate compound 16 (307 mg, 84% yield). Compound 16 has been obtained by elution of the column with 10% EtOAc/petroleum ether.
Data for compound 16 Rf = 0.4 in (10% EtOAc/ petroleum ether mixture): colorless solid: mp 118 oC; 1H NMR (400 MHz, CDCl3): δ 2.47 (t, J = 2.5 Hz, 2H), 3.94-3.97 (m, 4H), 4.18-4.21 (m, 4H), 4.18 (d, J = 2.5 Hz, 4H), 6.90-7.25 (m, 8H); 13C NMR (100 MHz, CDCl3): δ 57.32, 68.97, 70.07, 75.71, 79.11, 114.77, 116.09, 121.56, 122.74, 147.65, 149.44; HRMS (Q- TOF) m/z: [M+Na]+ calcd for C22H22O5Na 389.1359 found 389.1358; IR (KBr): υmax: 740, 1265, 1499, 2305, 2987, 3420 cm-1.
Synthesis of compound 8
Solution of dipropargylated compound 6 (366 mg, 1 mmol) in dry THF (15 mL) was maintained at -78 oC and n-BuLi (1.6 M solution in hexanes) was added to the reaction mixture. The reaction mixture was stirred for 3 h at the same temperature, and MeI (158 mg, 3 mmol) was added dropwise over a period of 10 min. Further, reaction mixture was stirred for 3 h. At the conclusion of the reaction (TLC monitoring), reaction mixture was brought to room temperature. Saturated aq. solution of NH4Cl was added and reaction mixture was extracted with EtOAc. The combined organic layer was washed with 4N HCl (2 Χ 100 mL), saturated aq. NaHCO3 (100 mL), water (2 Χ 200 mL) and brine (200 mL). The organic layer was dried over anhydrous Na2SO4, filtered and the solvent was removed on a rotavapour. The crude product was chromatographed on a silica gel column and elution of the column with petroleum ether/EtOAc mixture to afford the compound 8 (267 mg, 68% yield).
Data for compound 8 Rf = 0.3 in (10% EtOAc/ petroleum ether mixture):colorless liquid: 1H NMR (400 MHz, CDCl3): δ 1.85 (t, J = 2 Hz, 6H, 3.91-3.93 (m, 4H), 4.12-4.14 (m, 4H), 4.60 (q, J = 2 Hz, 4H), 6.53-6.57 (m, 8H); 13C NMR (100 MHz, CDCl3): δ 56.62, 67.64, 70.06, 74.15, 83.89, 102.17, 102.30, 107.49, 107.63, 129.99, 159.21, 160.07; HRMS (Q- TOF) m/z: [M+Na]+ calcd for C24H26O5Na 417.1677 found 417.1673; IR (neat): υmax: 740, 1265, 1422, 1597, , 2987, 3056 cm-1.
General procedure for Glaser–Eglinton coupling reaction
To a suspension of cupric acetate monohydrate (1 mmol) in MeCN (20 mL), pyridine (0.5 mL) was added and reaction mixture was heated to 60 °C and then a solution of the bis-propargyl ether 6 or (16) (0.5 mmol) in MeCN (20 mL) was added. The color of the solution changed from deep blue to green. The reaction mixture was stirred for 2 h and then cooled to room temperature, and water was added (50 mL). The mixture was extracted with CH2Cl2 (3 Χ 50 mL). The combined organic layer was washed with 4N HCl (2 Χ 100 mL), saturated aq. NaHCO3 (100 mL), water (2 Χ 200 mL) and brine (200 mL). The organic layer was dried over anhydrous Na2SO4, filtered and the solvent was removed on a rotavapour. The crude product was chromatographed on a silica gel column and elution of the column with petroleum ether/EtOAc mixture to afford the compound 4 or 17 as colorless solids.
Following the general procedure, 1 mmol (366 mg) of bis-propargyl 6 was subjected for Glaser–Eglinton coupling reaction to generate compound 4 (342 mg, 94% yield). Compound 4 has been obtained by elution of the column with 10% EtOAc/petroleum ether.
Data for compound 4 Rf = 0.3 in (10% EtOAc/ petroleum ether mixture):colorless solid: mp 135 oC; 1H NMR (400 MHz, CDCl3): δ 3.89-3.91 (m, 4H), 4.15-4.17 (m, 4H), 4.72 (s, 4H), 6.49-6.54 (m, 4H), 6.76 (t, J = 2.3 Hz, 2H), 7.18 (t, J = 8.2 Hz, 2H); 13C NMR (100 MHz, CDCl3): δ 56.48, 67.33, 69.55, 71.63, 74.82, 102.05, 105.96, 110.66, 130.09, 158.71, 160.04; HRMS (Q- TOF) m/z: [M+Na]+ calcd for C22H20O5Na 387.1203 found 387.1203; IR (KBr): υmax: 741, 1265, 1422, 1596, 2305, 2987, 3055 cm-1.
Following the general procedure, 1 mmol (366 mg) of bis-propargyl 16 was subjected for Glaser–Eglinton coupling reaction to generate compound 17 (296 mg, 81% yield). Compound 17 has been obtained by elution of the column with 10% EtOAc/petroleum ether.
Data for compound 17 Rf = 0.3 in (10% EtOAc/ petroleum ether mixture): colorless solid: mp 142 oC; 1H NMR (400 MHz, CDCl3): δ 4.00 (t, J = 5.5 Hz, 4H), 4.20 (t, J = 5.5 Hz, 4H), 4.72 (s, 4H), 6.90-7.01 (m, 8H); 13C NMR (100 MHz, CDCl3): δ 61.19, 68.83, 70.09, 71.02, 75.64, 115.49, 119.95, 121.95, 124.56, 148.05, 151.20; HRMS (Q- TOF) m/z: [M+K]+ calcd for C22H20O5K 403.0942 found 403.0942; IR (KBr): υmax: 739, 1265, 1455, 1601, 2923, 3054 cm-1.
General procedure for hydrogenation
The conjugated alkyne 4 (or 17) was dissolved in EtOAc and degassesd with nitrogen for 15 min. Then, 10% Pd/C was added to the reaction mixture, and the mixture was stirred at room temperature under a hydrogen atmosphere (1 atm) for 12 h. At the conclusion of the reaction (TLC monitoring), the solvent was evaporated under reduced pressure, and the crude product was purified by column chromatography to deliver hydrogenated product 7 (or 18).
Following the general procedure of catalytic hydrogenation, 1 mmol (364 mg) of compound 4 was subjected hydrogenation reaction to generate compound 7 (342 mg, 92% yield). Compound 7 has been obtained by elution of the column with 10% EtOAc/petroleum ether.
Data for compound 7 Rf = 0.4 in (10% EtOAc/ petroleum ether mixture): colorless solid: mp 102 oC; 1H NMR (400 MHz, CDCl3): δ 1.56-1.58 (m, 4H), 1.78 (t, J = 5.8 Hz, 4H), 3.90 (t, J = 4.5 Hz, 4H), 3.98 (t, J = 4.5 Hz, 4H), 4.13 (t, J = 4.5 Hz, 4H), 6.46-6.54 (m, 6H), 7.14 (t, J = 8.2 Hz, 2H); 13C NMR (100 MHz, CDCl3): δ 25.03, 28.10, 67.65, 67.89, 70.22, 102.87, 106.93, 107.14, 129.96, 160.22, 160.52; HRMS (Q- TOF) m/z: [M+K]+ calcd for C22H28O5K 411.1568 found 411.1564; IR (KBr): υmax: 741, 1265, 1422, 1597, 2987, 3055 cm-1.
Following the general procedure, 1 mmol (364 mg) of compound 17 was subjected hydrogenation reaction to generate compound 18 (334 mg, 90% yield). Compound 18 has been obtained by elution of the column with 10% EtOAc/petroleum ether.
Data for compound 18 Rf = 0.4 in (10% EtOAc/ petroleum ether mixture): colorless solid: mp 112 oC; 1H NMR (400 MHz, CDCl3): δ 1.60-1.62 (m, 4H), 1.83 (t, J = 5.8 Hz, 4H), 4.02-4.05 (m, 8H), 4.17 (t, J = 4.7 Hz, 4H), 6.90 (s, 8H); 13C NMR (100 MHz, CDCl3): δ 26.45, 29.68, 69.69, 69.84, 70.64, 114.95, 115.44, 121.58, 121.88, 149.41, 149.63; HRMS (Q- TOF) m/z: [M+Na]+ calcd for C22H28O5Na 395.1829 found 395.1829; IR (KBr): υmax: 707, 741, 1266, 1421, 2987, 3054 cm-1.
Alternative procedure to synthesis compound 7 and 18
To a stirred solution of bisphenol (5/12) (1 mmol) in MeCN (15 mL) was added K2CO3 (5 mmol) and the resultant suspension was stirred for 30 min. Then, 1,6-dibromohexane (3 mmol) was added dropwise over a period of 10 min. Further, the crude reaction mixture was stirred for 12 h at reflux. At the conclusion of the reaction (TLC monitoring), the crude mixture was filtered through celite pad (washed with CH2Cl2) and concentrated under reduced pressure. The crude product was purified by column chromatography. Cyclophane products (7 and 18) data obtained by this procedure was compared with data obtained by hydrogenation process.
ACKNOWLEDGEMENTS
The authors thank Council of Scientific and Industrial Research (CSIR), New Delhi and the Department of Science and Technology (DST), New Delhi for the financial support. Sophisticated Analytical Instrument Facility (SAIF), Mumbai is thanked for recording the spectroscopic data. G. T. W thanks CSIR for the award of a research fellowship. S. K thanks the DST for the award of a J. C. Bose fellowship. We thank the reviewers for the useful suggestions.
References
1. H. J. Reich and D. J. Cram, J. Am. Chem. Soc., 1969, 91, 3505. CrossRef
2. M. Sheehan and D. J. Cram, J. Am. Chem. Soc., 1969, 91, 3544. CrossRef
3. J. P. Sauvage and J. M. Lehn, Bull. Soc. Chim., 1970, 50.
4. D. J. Cram and J. M. Cram, Acc. Chem. Res., 1971, 4, 204. CrossRef
5. J. Cheney and J. M. Lehn, J. Chem. Soc., Chem. Comm., 1972, 487.
6. C. J. Pedersen, Angew. Chem., Int. Ed. Engl., 1988, 27, 1021. CrossRef
7. C. J. Pedersen, J. Inclu. Phenom., 1988, 6, 337.
8. P. Guerriero, S. Tamburini, and P. A. Vigato, Coord. Chem. Rev., 1995, 139, 17. CrossRef
9. O. Hayashida, J. Syn. Org. Chem. Jpn., 2006, 64, 1041. CrossRef
10. A. R. Bogdan, S. V. Jerome, K. N. Houk, and K. James, J. Am. Chem. Soc., 2012, 134, 2127. CrossRef
11. R. Zimmer, M. Taszarek, L. Schefzig, and H. U. Reissig, Synlett, 2008, 2046.
12. G. Yapar and C. Erk, J. Incl. Phenom. Macro., 2002, 43, 299. CrossRef
13. E. S. Hirst and R. Jasti, J. Org. Chem., 2012, 77, 10473. CrossRef
14. M. Shibahara, M. Watanabe, K. Aso, and T. Shinmyozu, Synthesis, 2008, 3749. CrossRef
15. F. Diederich and P. J. Stang, Templated Organic Synthesis, Wiley-VCH Verlag GmbH, 2007.
16. P. Wipf and M. Furegati, Org. Lett., 2006, 8, 1901. CrossRef
17. H. Okamoto, K. Satake, H. Ishida, and M. Kimura, J. Am. Chem. Soc., 2006, 128, 16508. CrossRef
18. H. Hopf and R. Gleiter, Modern Cyclophane Chemistry, Wiley-VCH Verlag GmbH & Co. KGaA, 2005.
19. C. M. Wei, K. F. Mo, and T. L. Chan, J. Org. Chem., 2003, 68, 2948. CrossRef
20. S. Kotha, G. T. Waghule, and M. E. Shirbhate, Eur. J. Org. Chem., 2014, 984. CrossRef
21. E. Weber and F. Vogtle, Justus Liebigs Ann. Chem., 1976, 891. CrossRef
22. S. Kotha and M. E. Shirbhate, Synlett, 2012, 2183. CrossRef
23. S. Kotha, A. S. Chavan, and M. Shaikh, J. Org. Chem., 2012, 77, 482. CrossRef
24. S. Kotha and K. Mandal, Eur. J. Org. Chem., 2006, 5387. CrossRef
25. S. Kotha, K. Mandal, K. K. Arora, and R. Pedireddi, Adv. Synth. Catal., 2005, 347, 1215. CrossRef
26. S. Kotha and S. Halder, ARKIVOC, 2005, iii, 56.
27. S. Kotha, S. Halder, L. Damodharan, and V. Pattabhi, Bioorg. Med. Chem. Lett., 2002, 12, 1113. CrossRef
28. S. Kotha and G. T. Waghule, J. Org. Chem., 2012, 77, 6314. CrossRef
29. S. Kotha, M. Meshram, and A. Tiwari, Chem. Soc. Rev., 2009, 38, 206. CrossRef
30. Z. Wang, Comprehensive Organic Name Reactions and Reagents, John Wiley & Sons, Inc., 2009, p. 959.
31. K. Jyothish and W. Zhang, Angew. Chem. Int. Ed., 2011, 50, 8478. CrossRef
32. G. Valot, C. S. Regens, D. P. O'Malley, E. Godineau, H. Takikawa, and A. Furstner, Angew. Chem. Int. Ed., 2013, 52, 9534. CrossRef
33. A. Fürstner, Chem. Commun., 2011, 47, 6505. CrossRef
34. B. Mao, M. Fananas-Mastral, M. Lutz, and B. L. Feringa, Chem. Eur. J., 2013, 19, 760.
35. C. Deraedt, M. d'Halluin, and D. Astruc, Eur. J. Inorg. Chem., 2013, 4881.
36. J. W. Li and D. Lee, Eur. J. Org. Chem., 2011, 4269. CrossRef
37. D. Castagnolo, L. Botta, and M. Botta, J. Org. Chem., 2009, 74, 3172. CrossRef
38. S. Beer, K. Brandhorst, J. Grunenberg, C. G. Hrib, P. G. Jones, and M. Tamm, Org. Lett., 2008, 10, 981. CrossRef
39. W. Sim, J. Y. Lee, J. S. Kim, J.-G. Kim, and I.-H. Suh, Acta Crystallogr. Sect. C, 2001, 57, 293. CrossRef
40. S. Kotha, R. Ali, and A. Tiwari, Synlett, 2013, 24, 1921. CrossRef
41. S. Kotha and P. Khedkar, Chem. Rev., 2012, 112, 1650. CrossRef
42. S. Kotha and A. S. Chavan, J. Org. Chem., 2010, 75, 4319. CrossRef
43. S. Kotha, D. Kashinath, and P. Khedkar, Synthesis, 2007, 3357. CrossRef
44. S. Kotha, P. Khedkar, and A. K. Ghosh, Eur. J. Org. Chem., 2005, 3581. CrossRef
45. M. Srinivasan, S. Sankararaman, H. Hopf, I. Dix, and P. G. Jones, J. Org. Chem., 2001, 66, 4299. CrossRef